Demand for Manufacturing Training Services in Bangladesh
- Managers
- Productivity
- Take-up of program/social service/healthy behavior
- Business skills training
Increasing factory productivity is an important channel for growth and poverty reduction in low- and middle-income countries, and consulting and training programs are a promising tool to do so. Yet, there is a limited market for these services in some contexts, including in Bangladesh. Researchers are partnering with the German Society for International Cooperation (GIZ) to identify barriers to a wider market for consulting and training in Bangladesh by offering high-quality manufacturing training services at randomly-assigned price points and covering different topics. They find that factories and managers are unwilling to take-up high-quality training services more as a result of high production pressures than as a result of high prices, and that there is higher demand for training to improve production planning and quality than for training on human or social resources.
الموضوع الأساسي
Increasing factory productivity can drive economic growth and poverty reduction. Resource-intensive management training programs are one promising tool to enhance productivity. Yet, there is a limited market for these services in many contexts, including in Bangladesh. These programs could become more affordable and sustainable if there were a wider market for them. Researchers are trying to identify the barriers to a wider market for management training by offering high-quality training to low-level managers at different price points and covering different topics.
سياق التقييم
In Bangladesh, more than 3,000 garment exporting factories employed as many as 150,000 line managers at the time of this study. Managers in these factories face high pressure to produce. As a result, manager time is often extremely limited, including by the need to respond to shocks arising from fast production methods that deliver finished products right when they are needed to out-compete similar rivals and economize on costs. The combination of high pressure, tight timelines, and limited managerial training and ability can result in relatively low productivity and bad labor relations.
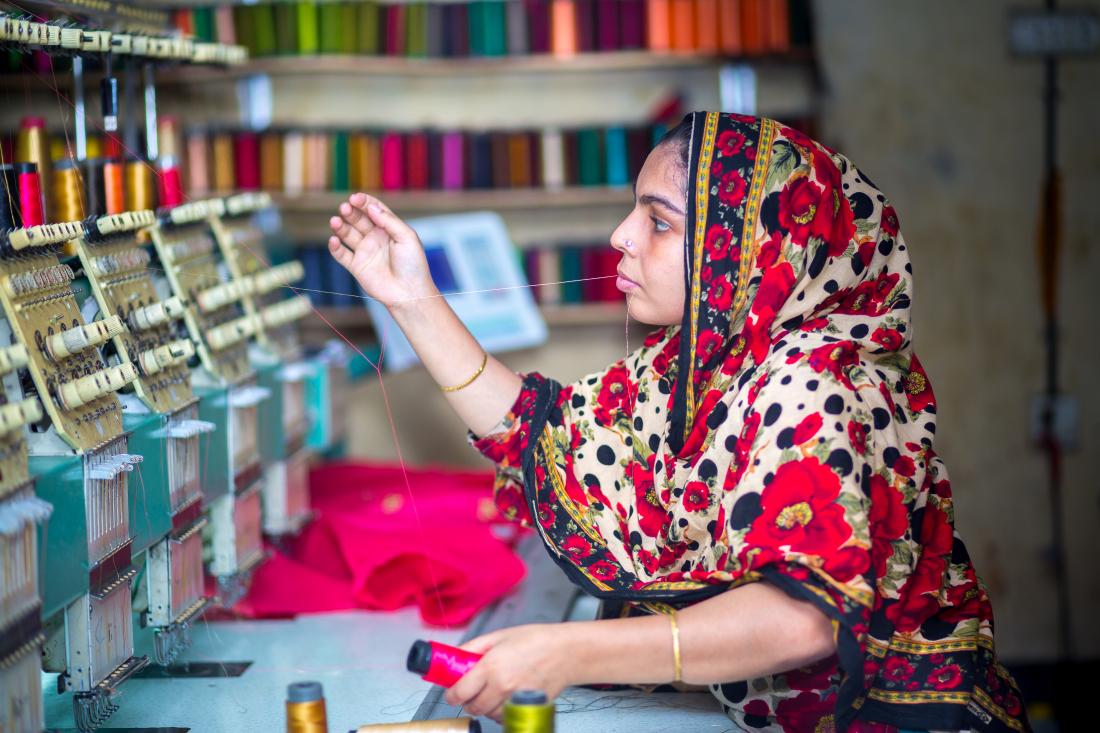
معلومات تفصيلية عن التدخل
Researchers partnered with a local service provider and the German Society for International Cooperation (GIZ) to evaluate the impact of pricing and training content on firm-level take-up of management training. The study sample included 288 factories in the garment exporting industry; however, only 183 decision makers were reached, and only 135 received the initial pitch from the research team. The research team offered factories a six-day training program for their line managers, covering three groups of topics: production planning and processes; quality enhancing processes; and human resources, leadership, and social compliance. The training program was offered at randomly-assigned price points, ranging from 60 to 100 percent of the actual program cost, and the researchers also randomized one of the three modules to be offered to each factory for free. Researchers called factories initially and for follow-up and measured whether the points of contact at the factories:
- Requested that more information about the training program be sent by mail.
- Took-up their free module in the training program.
- Asked questions about the training program, and/or turned the program down.
النتائج والدروس المستفادة بشأن السياسات
Demand for more program information was high, but only sixteen factories (6 percent) in the original sample ultimately accepted the free training module. Why were factories turning down free, high-quality training from a trusted source?
Factories were relatively insensitive to price, both in requesting more information and in taking up the program. However, a higher price did lead factories to ask more questions about the program during follow-up calls.
Factories were more likely to request program information when they were offered the training modules covering either the production planning and processes or the quality enhancing processes for free. Yet, factories asked many more questions about logistics than about either program content or pricing.
Among factories that gave concrete reasons for refusing the program, production pressure and limited manager time were the two leading reasons. Participants also reported feeling concerned about having managers trained off site, that the training would be ineffective, that trained managers would leave for other factories, or that training would take too long.
This evidence suggests that there could be a viable market for management training if the largest non-price barriers were eliminated, including constraints on managers’ time, given that price was not the main deterrent to factories in taking up training. In contexts similar to this one, demand for management training could be higher if programs focused on production planning and quality enhancement, and better accounted for line managers’ high-pressure and time-constrained work environments.